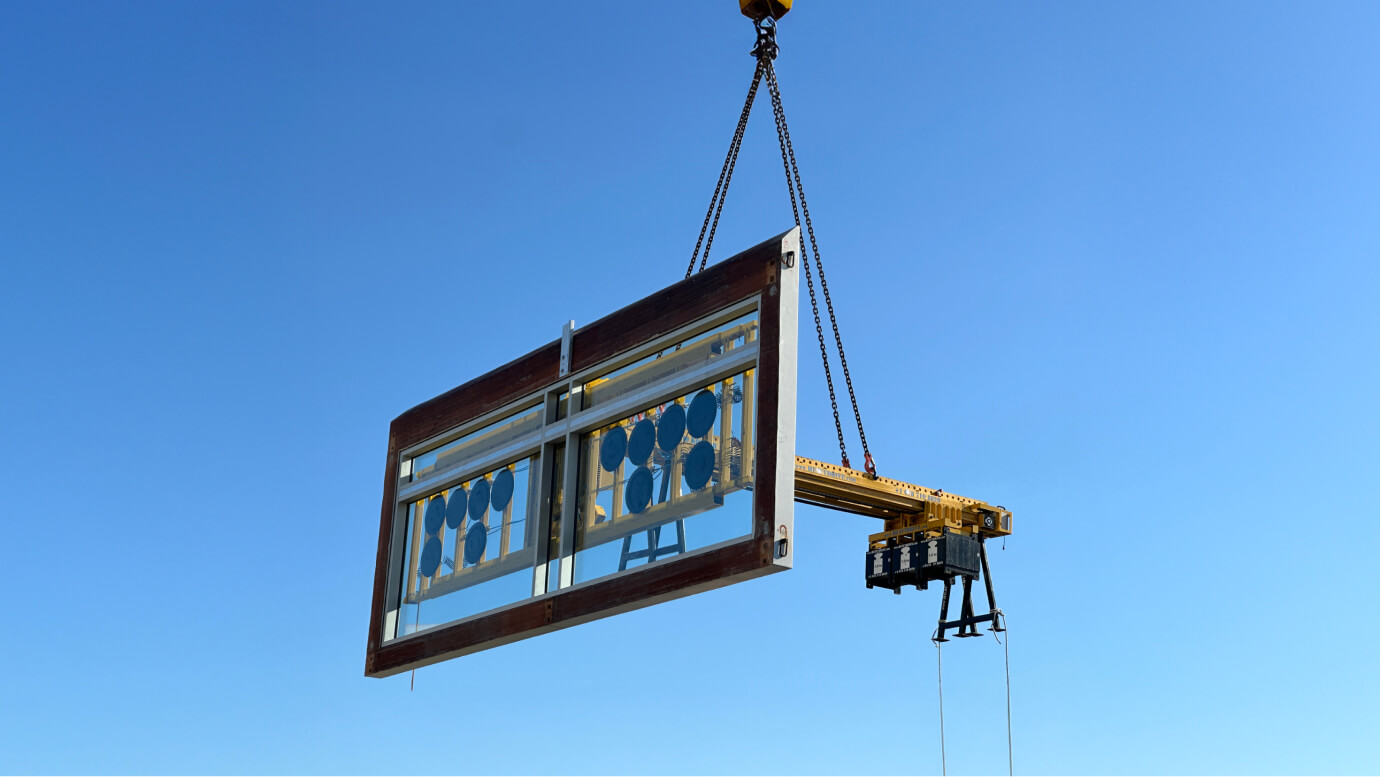
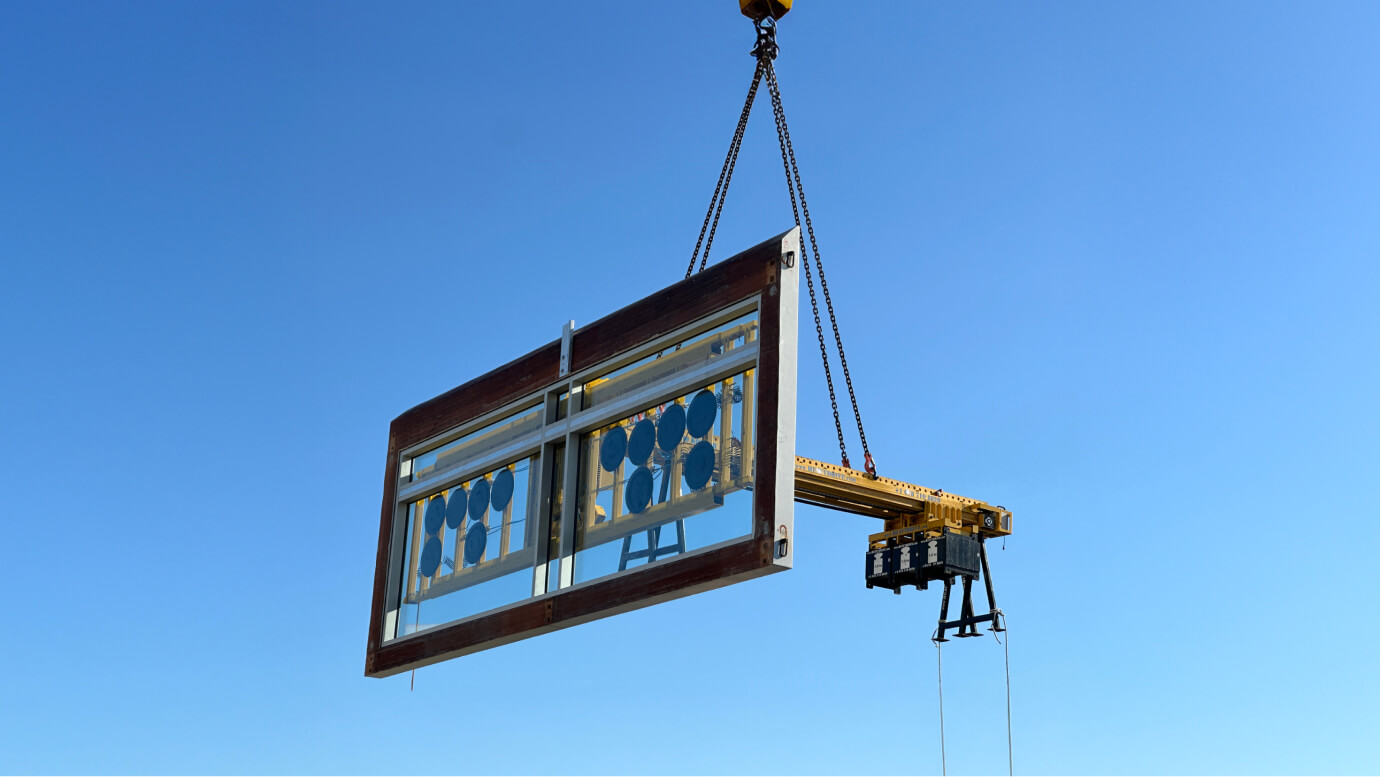
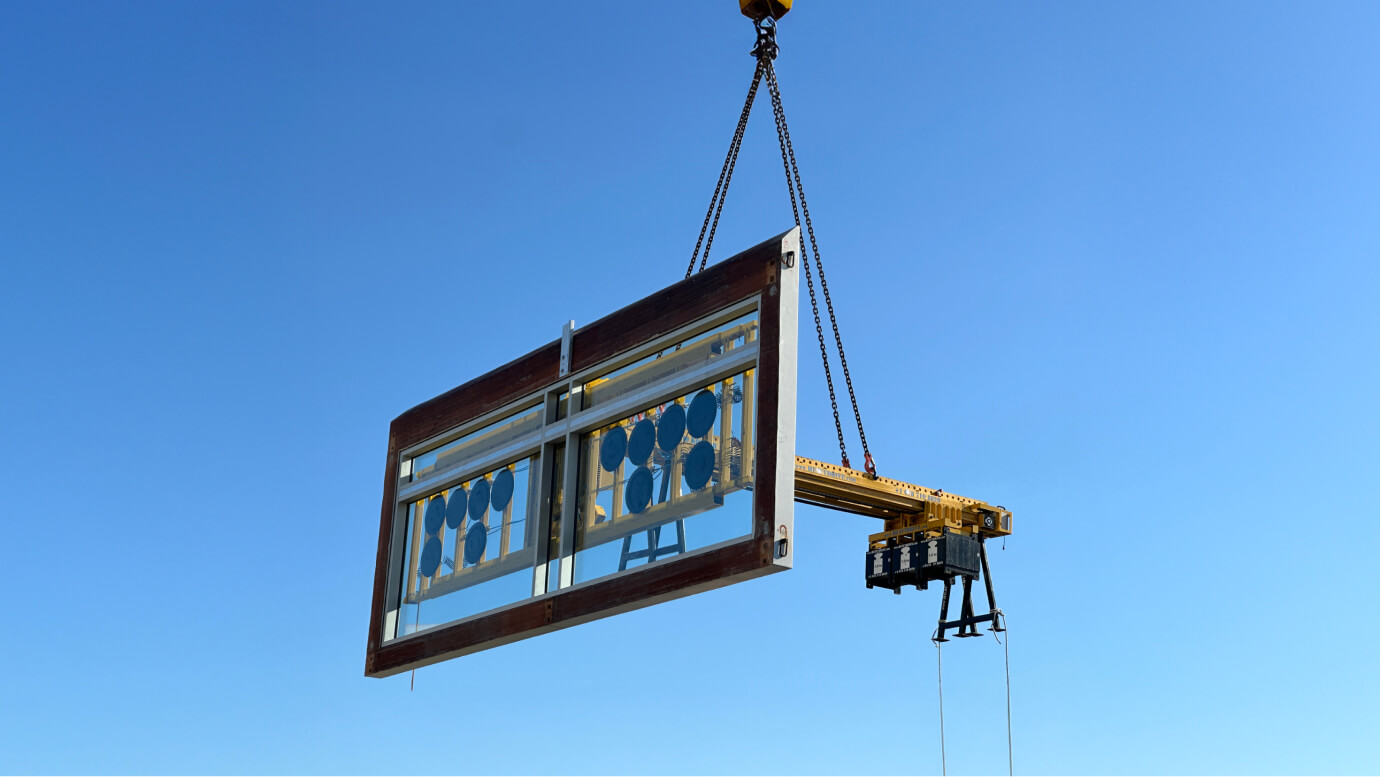
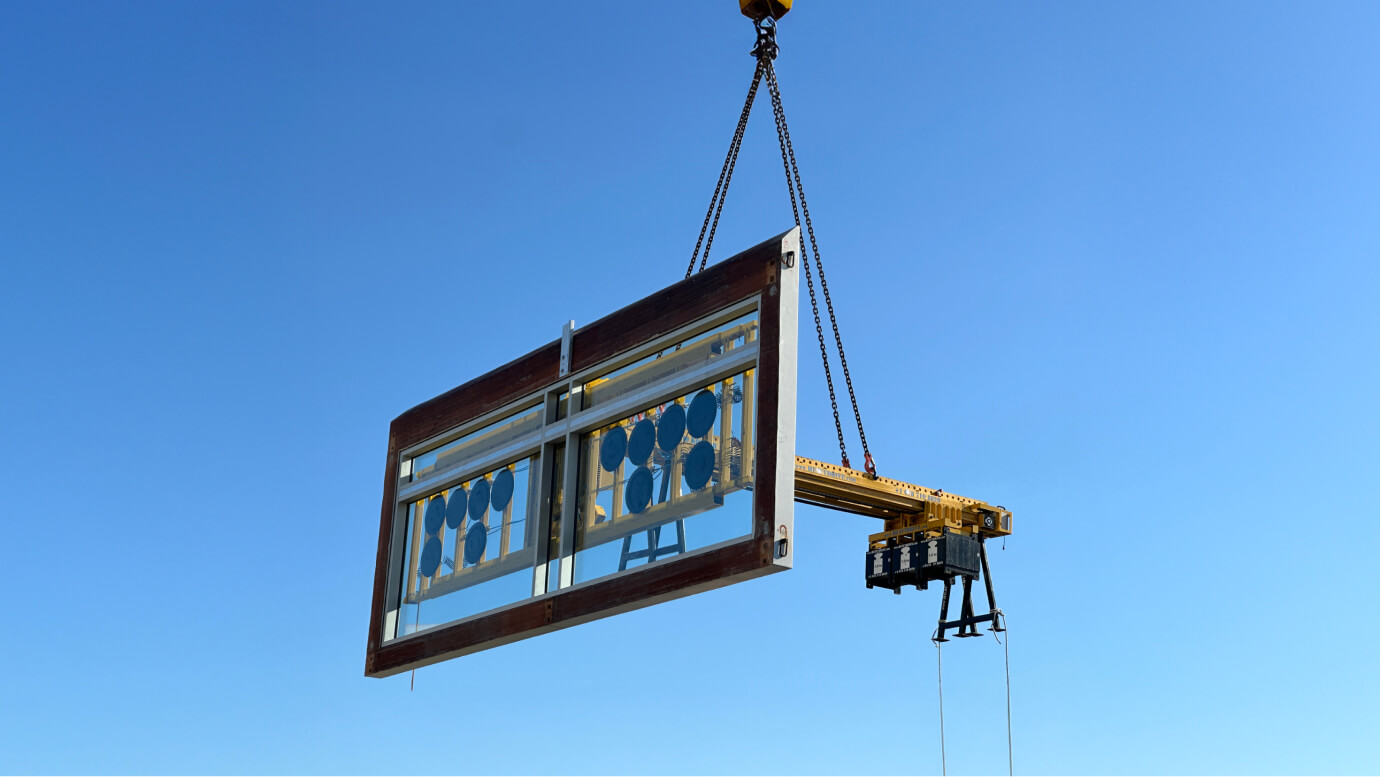
HyperWall exterior building skin panels from Building Composites are considerably lighter than precast concrete equivalents — typically 8 to 16 psf. This weight difference offers numerous benefits, ranging from faster installation to safer job sites and more sustainable structures. Most importantly, however, every advantage derived from the light weight of HyperWall panels delivers potential savings, reducing your cost basis.
Here’s a quick summary of the many ways architects, developers, contractors and building owners can benefit and save with lighter HyperWall panels.
Compared to precast concrete, three times as many HyperWall panels can be transported per truck, reducing the total number of vehicles needed. Transport will be further simplified by detachable A-frames with lift points. These frames don’t need to be built into the truck because the panels are lightweight. Minimal structural connections to the truck bed make it easy to load and unload the A-frames. Once panels are delivered, A-frames can be stacked onto a return truck for future use.
Detachable A-frames enable Building Composites to use third-party common carriers for delivery, significantly reducing your freight costs. Unlike many precast concrete vendors, Building Composites doesn’t need to maintain its own fleet or drive trucks back to a facility after panels are delivered. Transportation services can be bid out, lowering costs further. This simplifies scheduling, because third-party trucks can be booked as needed. It also allows Building Composites to service all of North America, not just a limited region.
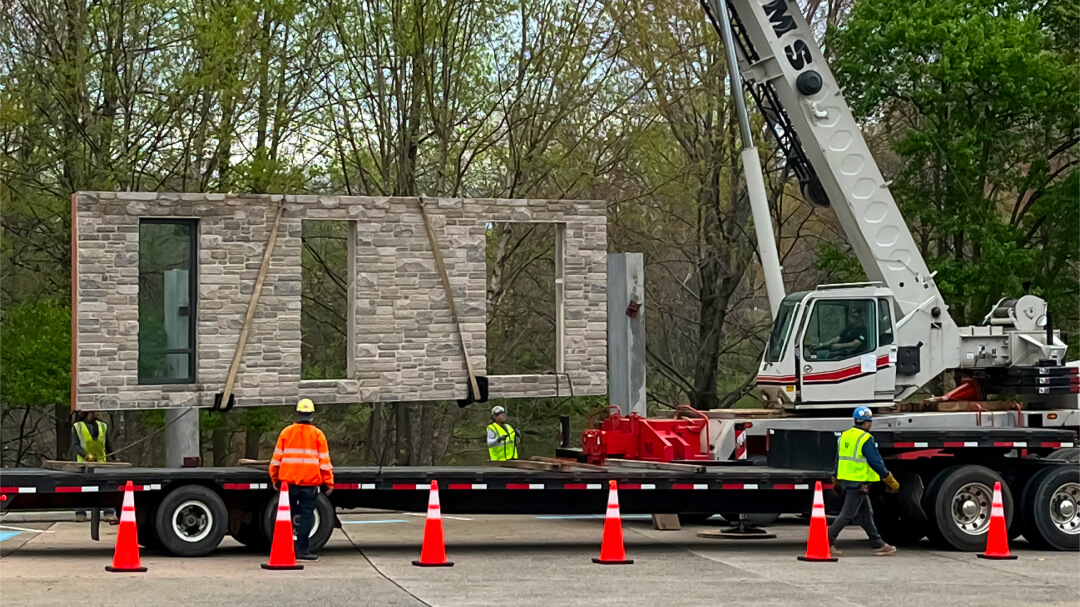
Lift points on the A-frames allow them to be quickly removed from flatbed trucks on-site, minimizing the time needed to unload while reducing congestion, both on the job site and in the surrounding area. This is especially advantageous in dense urban areas and other locations where a job site may require temporary street closures or other restrictions on when trucks can be brought in.
Lighter-weight panels give you more options when it comes to moving and handling them on a job site. Contractors can use less-expensive and lighter-weight cranes. For example, tower cranes could be used instead of rough terrain (RT) or crawler cranes.
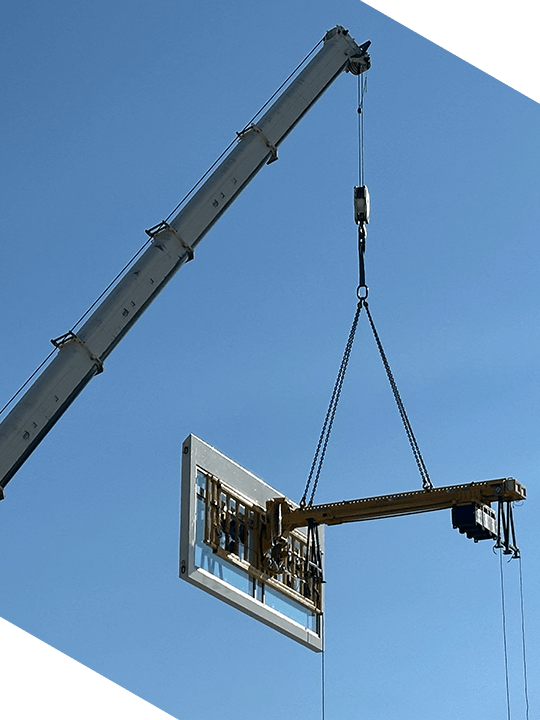
Cranes may not even be necessary at the ground floor level because HyperWall panels are light enough to be lifted by construction forklifts. Panels with pre-installed, large-format glazing can even be moved with a vacuum lifter, enabling more precise movement and eliminating the risks of spinning. These alternatives can free up higher-demand equipment like tower cranes to focus on different priorities and keep other trades working.
In addition to equipment flexibility, other factors contribute to speed. HyperWall panels can be mounted with lighter, bolted connections, which go together faster without welding.
Eliminating welding gives contractors more options for installers on the job site by reducing costs and scheduling hassles. It also allows connection points to be located closer to the edge of the building, potentially increasing rentable square footage compared to using precast panels in the same footprint.
Because less weight is being transmitted through the building frame, fewer connection points are needed. Designers have more options for where and how HyperWall panels can be connected to the building, further speeding up installation.
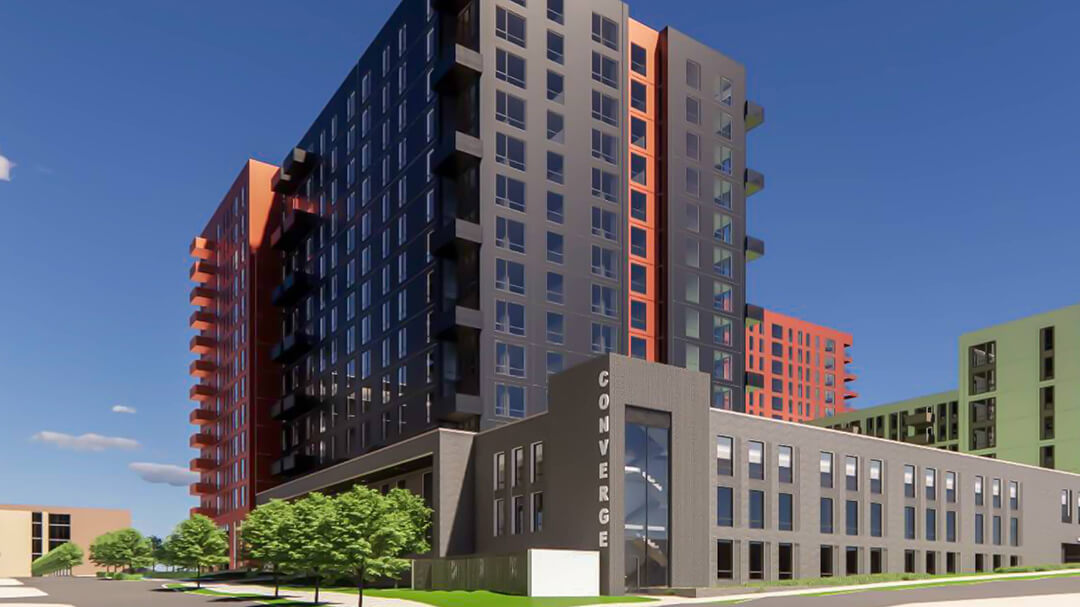
A-frame crane lift points minimize the time workers are above ground level when loading and unloading flatbed trucks. Reducing the number of trucks on or near active job sites lowers accident risks, especially in dense urban areas where unloading needs to happen quickly and visibility may be restricted for crane operators and drivers.
Lighter panels are easier to maneuver and seat correctly, and accident risks are eliminated when it’s possible to move them without cranes. In addition, pre-glazing and integrated waterproofing reduce the number of trades and worker hours on job sites, lowering the potential for safety incidents.
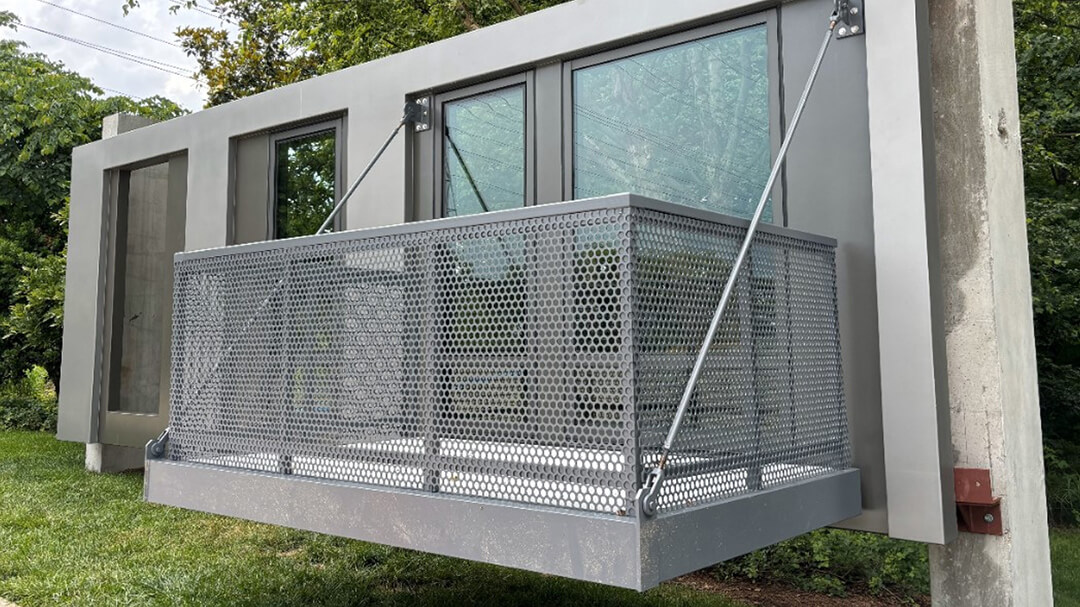
Lighter load weights and fewer total trucks reduce fuel consumption, costs and emissions. On-site equipment requires a fraction of the fuel or energy load, and lighter panels enable some sites to use electric, rather than diesel, equipment. Less congestion minimizes truck idling and associated emissions, especially in hot or cold weather.
All these advantages add up to less embodied carbon for the job. They also help the total project from a LEED perspective by allowing you to quantify the savings derived from using HyperWall panels in place of other materials.
As noted at the beginning of this article, every advantage made possible by the light weight of HyperWall panels reduces your costs. You benefit from all of them:
- Lower freight costs
- Less-expensive equipment needed on-site
- Faster installation
- Fewer on-site trades
- Lower accident risks
- Quantifiable sustainability
- Additional rentable square footage
Lighten Your Panels,
Lighten Your Loads
As we’ve shown, the HyperWall exterior building skin system offers appreciable advantages when compared with heavier, bulkier precast concrete solutions. From lower total costs and easier scheduling to flexibility, safety, sustainability and more, HyperWall panels deliver a competitive edge from start to finish.