Discover the HyperWall™ System
Speed, Sustainability and Lower Project Costs
The HyperWall system offers an innovative approach to building construction that combines HyperWall panels with pre-installed glazing and on-site installation. It’s a complete exterior structural/architectural building skin system that allows faster-constructed buildings, with fewer trades and subcontractors to coordinate on-site.
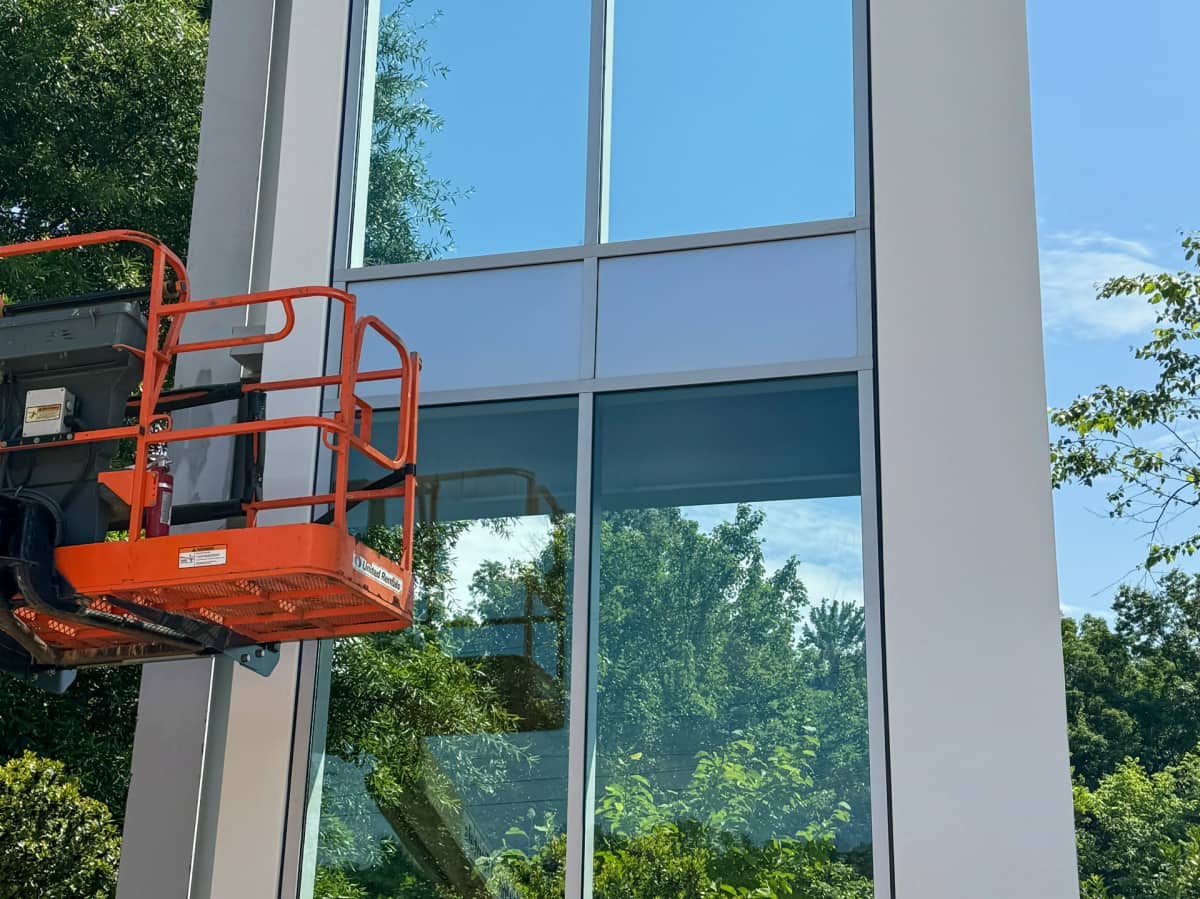
Reduce Embodied Carbon by up to 50%
HyperWall features the lowest embodied carbon of any building skin wall system on the market, reducing the total carbon footprint of any project. Glazing, waterproofing and other features can be integrated into the panels before they ever get to the job site.
Reduce On-site Trades
With typical R-values of 2 ft²·°F·h/BTU per inch, HyperWall provides superior thermal resistance — with no loose insulation to enclose. Vapor and moisture barriers are inherent to the panels, so no additional waterproofing is required.
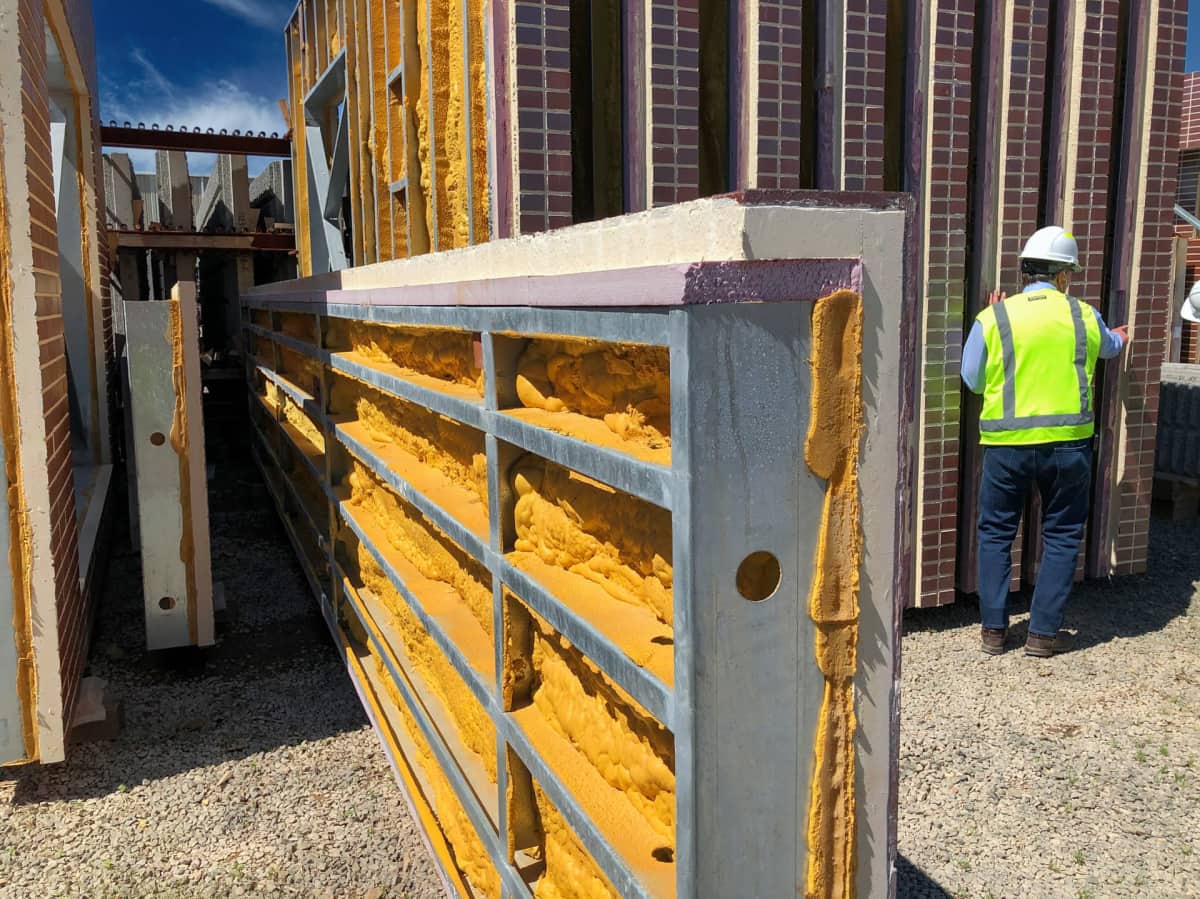
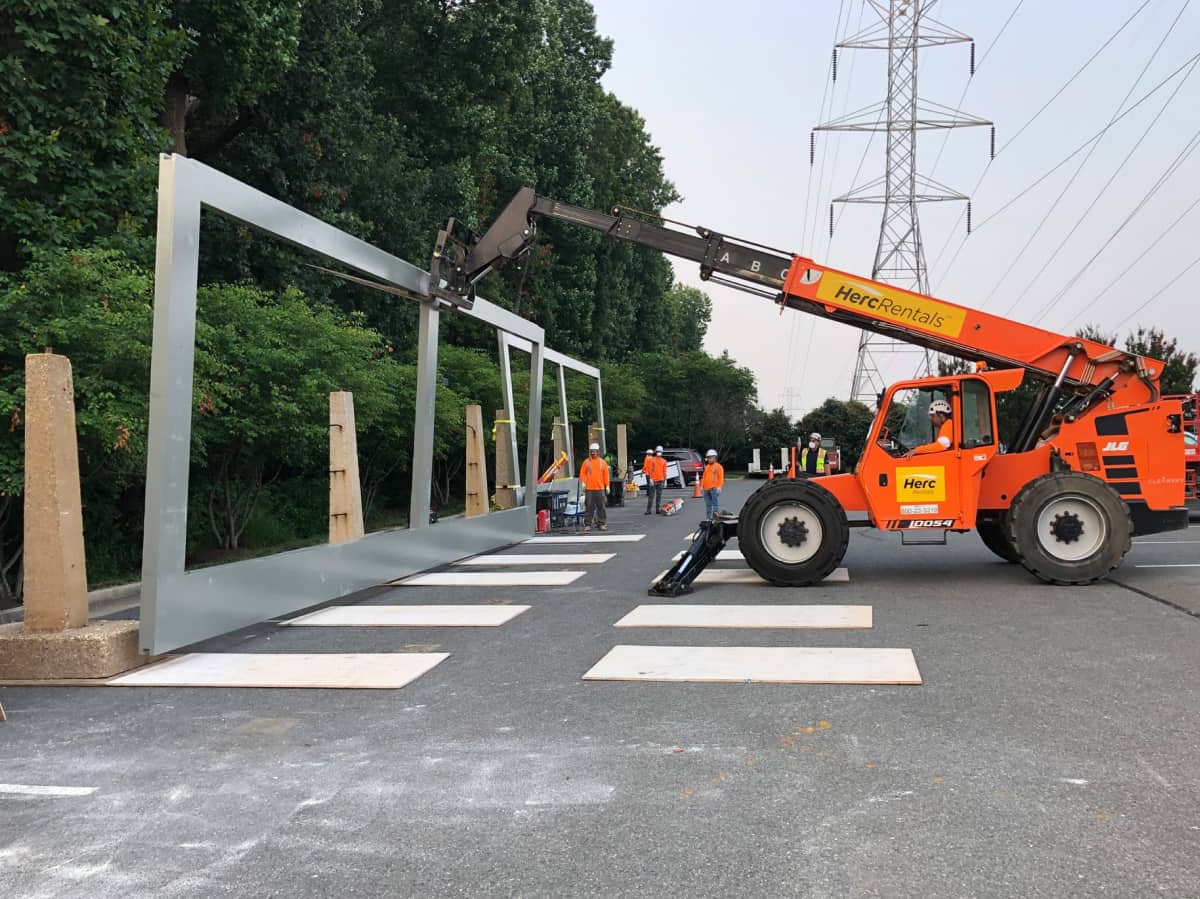
Save on Equipment
The lightweight nature of the system also translates to savings on equipment costs. Panels on the bottom level of a building can be set with mobile forklifts and higher levels with tower cranes, minimizing or eliminating the need for expensive and polluting diesel-powered mobile cranes.
Create Distinctive Designs Without Custom Costs
Significant investments in automation enable Building Composites to manufacture standardized and modular panels with high degrees of design flexibility while remaining cost-competitive. The opportunities for creative expression are unmatched by any other major construction material, enhancing your ability to create unique and distinctive projects.
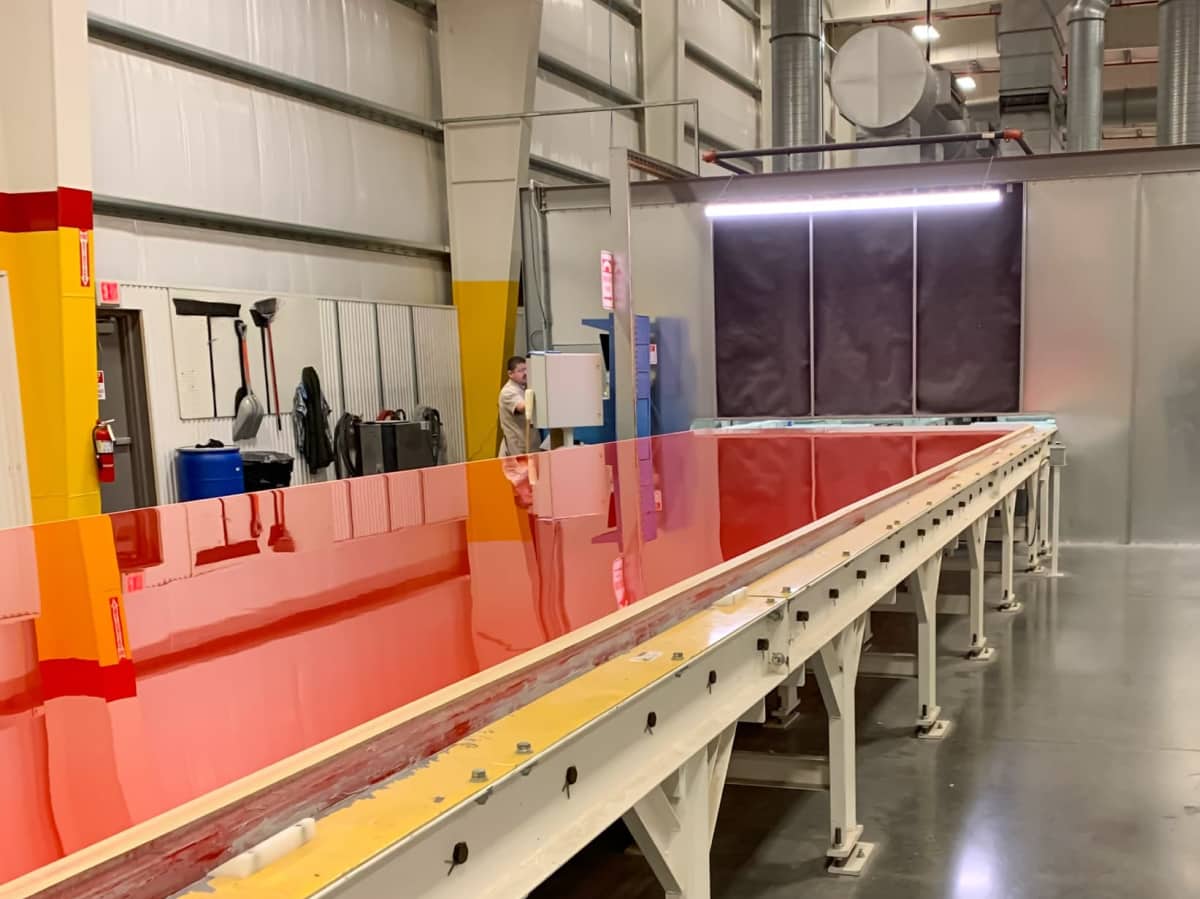
HyperWall Advantages
Designed to Solve Key Industry Challenges
Building Composites is dedicated to a vision of making building construction faster, more sustainable and less expensive. Specifically, the R&D team set out to meet the following goals:
- Reduce on-site labor
- Reduce construction time
- Reduce installed building skin wall costs (compared to architectural pre- cast concrete)
- Reduce timelines to enclose buildings by 33%
- Reduce embodied carbon by at least 50%
- Reduce the need for high-risk work on scaffolds and in bucket lifts
- Enable architects to achieve more innovative building designs
The team spent several years researching many different materials and systems. Seven technologies were eventually selected for testing on a demonstration building erected in Manassas, Va., near Dulles International Airport. The building was later moved and donated to Virginia Tech, where it is now used for research projects by their building construction department.
Ultimately, an all fiber-reinforced polymer (FRP) composite panel system stood out to the R&D team for its light weight, simplicity, versatility and cost-competitiveness. Further research verified that the FRP system could meet the goals of the project, satisfy all relevant building codes, and offer a practical alternative to other technologies.
Now in commercial production, HyperWall is being utilized by leading construction, architecture and development firms in advanced, sustainability-focused projects.